P.A.T. had been purchasing a pre-manufactured component for an assembly that they were contracted to perform for GE Aviation. The component was a silicon die within a housing that had a failure rate of approximately 20 percent upon receipt and yielded only 50 percent after potting and final testing of the assembly.
PAT was absorbing the cost of the failed part, frustrated by the high failure rate, and concerned about the possibility of post-assembly failures in the field.
Thomas Gulotta, President of P.A.T., believed the best way to solve the failure issue was to bring the production of the component in-house and have complete control of the process. After deciding to bring the assembly in-house with the installation and implementation of the Essemtec FOX2 system, Heller reflow oven and an ABS molding machine, P.A.T. was able to gain total control of the assembly process.
Mr. Gulotta stated, “bringing this process in house at P.A.T., we are able to produce 500 components per day with less than a 1% failure rate, all on a sophisticated but easy to use platform. The dispensing of the solder beads and placement of the die are now handled by the Essemtec Fox2, our standard Heller reflow oven, and our ABS molding machine. Our customer, GE Aviation is extremely pleased with the results of this new process”.
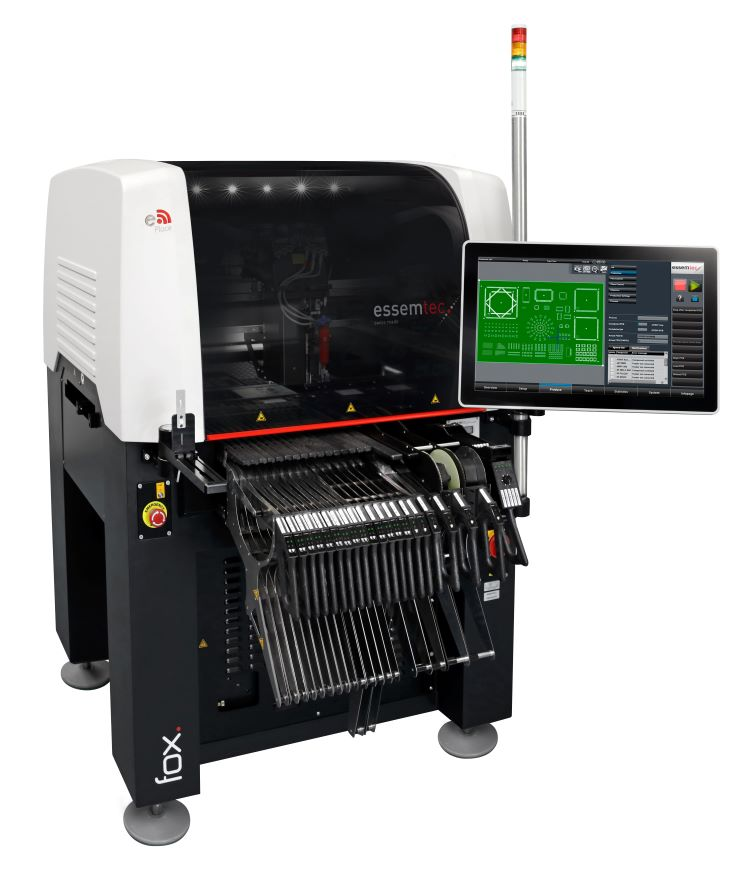
Precision Assembly Technologies is an AS9100 certified Aerospace and Defense Contract Manufacturer, specializing in full cutting-edge turnkey electronic manufacturing solutions. While supporting global industry leaders in the aerospace and defense sector, P.A.T. focuses on partnering with its customers to meet their quality, technology and service initiatives. For more information, visit www.pat-inc.com.