Precision Assembly technologies recently made a switch in our technology to help increase our volume of output for our products. We have implemented a new screen printer into our process, the MPM Momentum. This switch comes at the need for an increase in efficiency and reliability to the equipment we use to make our boards. The MPM momentum is recognized as a very reliable printer due to its newly designed welded steel frame. This frame’s axes are driven by precision ball screws, rather than the competitors belt driven axis. MPM’s design combining both the axes and the steel frame allow for fewer vibrations which leads to two major effects. Fewer vibrations call for less errors on the stencil prints, which allows for an increase in repeatability amongst all our boards. The precision ball screws also require no calibration which is why the MPM momentum is said to have a useful life of 10+ years, compared to competitors printers placing a minimum life of 3 years on their printers. The implementation of the MPM momentum has allowed P.A.T to greatly improve our board-making process by increasing our volume of output with greater efficiency and accuracy, as well as removing certain fixed costs associated with our production.
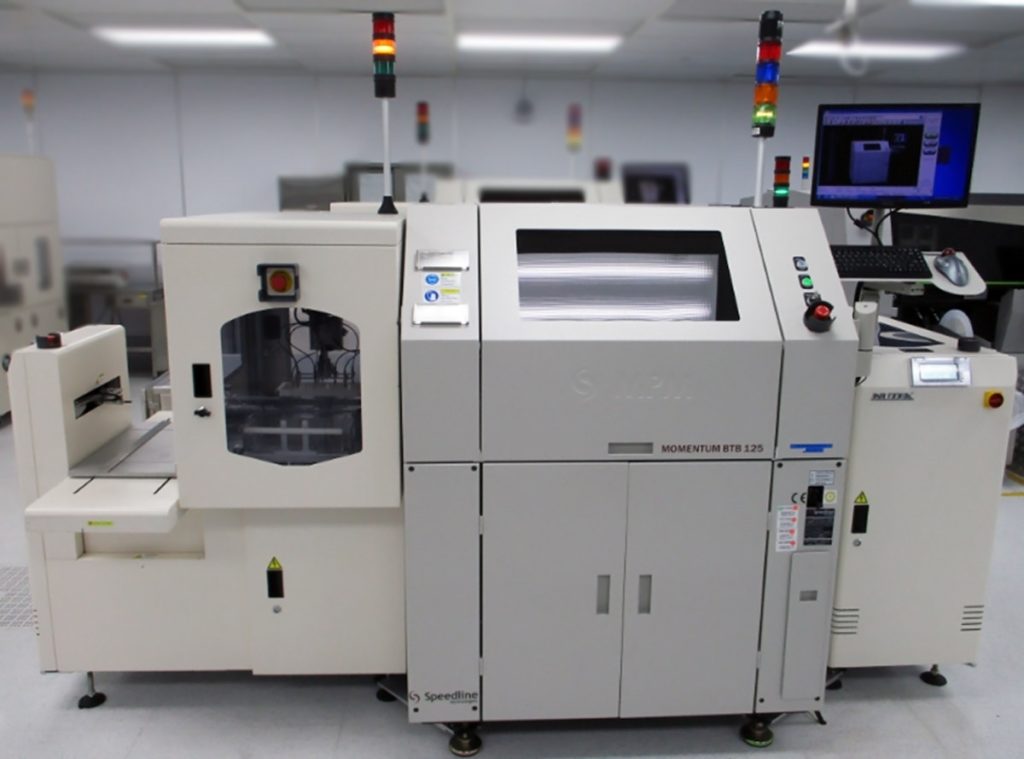